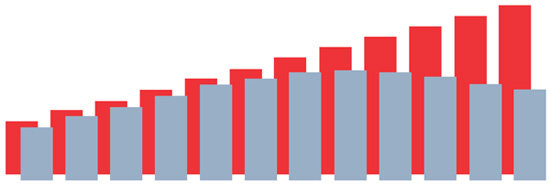 |
Greater eco-efficiency with a systematic approach and innovation
How can the global economy continue to grow when limited by finite natural resources? We have to decouple growth, energy demand, and resource consumption!
Energy efficiency is a mega-topic all around the planet. The new EU Energy Efficiency Directive, which went into effect in June 2012, demands that member states reduce energy consumption at a rate of 1.5 percent per year. Despite its building many new power plants and expanding wind energy, China can hardly keep up with the rise in demand. The twelfth Chinese five-year plan thus prescribes that energy intensity (units of energy per unit of gross domestic product) be reduced by 16 percent by 2015. Japanese industry – more or less overnight and after the country’s 50 atomic power had been shut down – was forced to permanently reduce its power consumption by 15 percent. And Brazil intends to reduce its greenhouse emissions by 36 percent no later than 2015.
There’s a long way to go before the industrialized world’s energy requirements can be met with renewables. A major portion of the world’s electrical power is still generated by burning fossil fuels including natural gas, petroleum and coal. Consequently, efficient use of energy is the most effective way to reduce CO2 emissions, to protect the environment, and to rein in rising costs. It is in Asia, in particular, that companies in every industry are clearly demanding higher energy efficiency in machinery and equipment. This is the only way to satisfy government standards and, at the same time, offset electricity price rises. That is why successful measures to achieve greater energy efficiency are implemented quickly and universally. In China, for instance, more and more manufacturers are using variable-speed pump drives by Rexroth and in so doing reducing by up to 70 percent the amount of energy used by hydraulic systems in plastic manufacturing machines or machine tools. These solutions are also compatible with existing machinery concepts; machines are often refitted with such pumps.
Customers expect that new machines will deliver even higher energy efficiency at maximum productivity. This is one reason why specifications ever more frequently include up-per limits for the connected load. To meet expectations for energy efficiency, design engineers will have to keep an eye on later energy consumption right from the concept phase. Helpful here are systematic methods like Rexroth 4EE (Rexroth for Energy Efficiency). This approach is effective for all drive and control technologies and takes equipment interdependencies into account. This is especially important since otherwise energy savings at one location can drive up consumption at another point. This system can be applied not only to new machinery designs; it is also suitable for analyzing the energy efficiency of existing manufacturing lines and even complete factories. In numerous projects – from the automotive industry to the preparation and packaging of foods – companies have already significantly reduced energy use while still achieving at least the same output. |
Less consumption with more innovation
Innovative software functions represent an important factor in reducing energy and material consumption. Rotary printing presses provide one example. In the past mechanical linkages, clutches, couplings, and gearboxes connected the individual rollers with the central motor. All that’s needed today is a communications cable. Software synchronizes the rollers without wear and at the utmost precision. The mechanical components for the main shaft are eliminated entirely. A further effect is improved versatility and precision. In packaging lines, presses, and assembly lines, too, “electronic shafts” are handling tasks that were previously executed mechanically.
Especially as production runs become shorter, the software reduces the reject rate when production is started and, at the same time, saves energy and material. Over and above that, engineers can design machines so they are smaller and lighter in weight. The Rexroth 4EE system, suitable for universal use, is employed right from the machine’s initial design phase. It uses simulation models to achieve the best possible design. Energy-efficient products and systems and recovering energies wasted to date, by way of recuperation and storage, round out the measures in the program. |
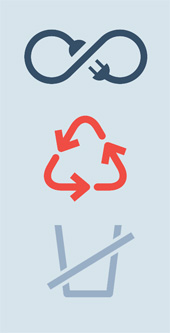 |
Totally efficient
A new punch press made by the Trumpf mechanical engineering company offers increased productivity and lower consumption of materials and energy. In the past a bulky, Lshaped scrap strip was left after punching parts from a panel of sheet metal. That strip had to be removed by hand. This new machine, by contrast, works its way across the panel, row by row, rather like nibbling at a bar of chocolate. It immediately sorts the punched parts and the scrap from each row.
This does not take any longer but the power consumed, when compared with previous designs, drops by about 25 percent, thanks to the Smart Energy Mode. Buffer storage in the intermediate circuit stores excess energy in a capacitor. That energy is then used to support acceleration. Punching without a scrap skeleton reduces material consumption by ten percent on average and in some cases by even as much as a third. Trumpf achieves this with several innovations, including a decentralized drive and control concept by Bosch Rexroth. The IndraMotion MTX, a CNC-based system solution, positions and controls the machine’s main axes. The drive-based IndraMotion MLD motion logic system is used in the punching head.
4wD with automatic activation
Combining ideal energy efficiency with the greatest possible ground traction often represents a “conflict of interests” in all-wheel-drive vehicles used by municipalities and as work vehicles. With its High Efficiency Traction Control – HET – Rexroth is introducing a hydrostatic drive train solution that satisfies both requirements. The energy efficiency of the HET is based in part on the fact that the wheels are driven only as needed. And switching is fully automatic, without
driver intervention. If a wheel loses traction in difficult terrain, then slippage rises quickly. The increasing flow of hydraulic fluid causes the torque to be transferred immediately to the second wheel motor in the circuit. With this “slippage activation” of the all-wheel drive function, the HET makes sure the vehicle will operate reliably off the road and, when compared with permanent AWD, makes for significant energy savings. |
More growth = more resource consumption? |
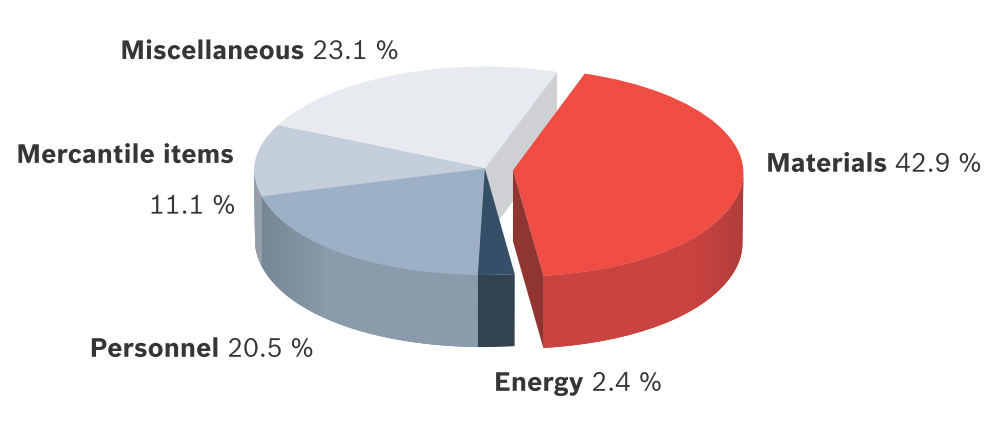 |
The scarcity of raw materials and feedstocks is a subject that will assume a significance similar to that now held by energy supplies. A current study by the Commerzbank, during which more than 4,000 companies were surveyed, showed that business is highly aware of the problems involved here. Given the fact that the share of manufacturing costs accounted for by materials is 40 percent or more, many companies view with concern the developments on the world’s raw materials markets. The options for meeting these challenges on the purchasing side – by instituting clever quantity policies or concluding longterm contracts, for instance – are very limited. Thus the problems arising from scarcity, rising prices, and volatility are often simply passed along to suppliers and customers. But these simple business administration techniques are insufficient to combat the effects of global resource shortages. The goal essentially has to be divorcing growth from resource consumption. The pressure for corrective action encountered by the manufacturing industry thus rises continuously.
Similar to energy efficiency, such activities may also be triggered by government regulations. The inevitable question here is how customer utility, sustainability and costs can be brought into line. Recent years’ successes in boosting energy efficiency show that – provided that a systematic procedure is followed – new ideas, business sectors and marketable innovations can quickly come into being. That is the view shared by the respondents in the Commerzbank study. “More innovation” was the most frequent solution mentioned in response to the question concerning the impact of shortages on middle-market companies. |
How can materials efficiency be increased?
Resources efficiency is a complex topic and, as a consequence, isn’t usually a “natural” in most companies. It is often necessary to first develop awareness for efficiency in using materials and for the potentials that result from that. It is a matter of scrutinizing the entire process, from placing the order to delivery. Here a number of parameters and process steps will play a role. Hidden contexts impede any simple identification of the mechanisms responsible for losses. According to the German Materials Efficiency Agency demea, critical leverage for the increase of materials efficiency is found in the fields of product design, manufacturing process, the production setting, and recycling. |
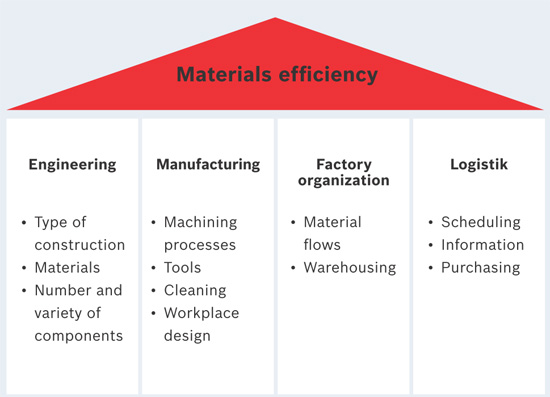 |
|