Packed with power
The engineers at Bosch Rexroth have successfully packed more power into a smaller motor. The Hägglunds CBM direct-drive hydraulic motor weighs only half as much as its predecessor, is smaller in size, and still generates 50 percent more torque, giving it the world’s best torque-to-weight ratio. This also makes it suitable for smaller, lighter and simpler equipment. The motor was developed in direct response to wishes expressed by customers. Especially when harvesting power from the wind and tides, a powerful motor is a basic requirement. In addition, the engineers made sure that the drive could be easily installed and refitted. As a result, the CBM satisfies the most exacting requirements of today’s market. |
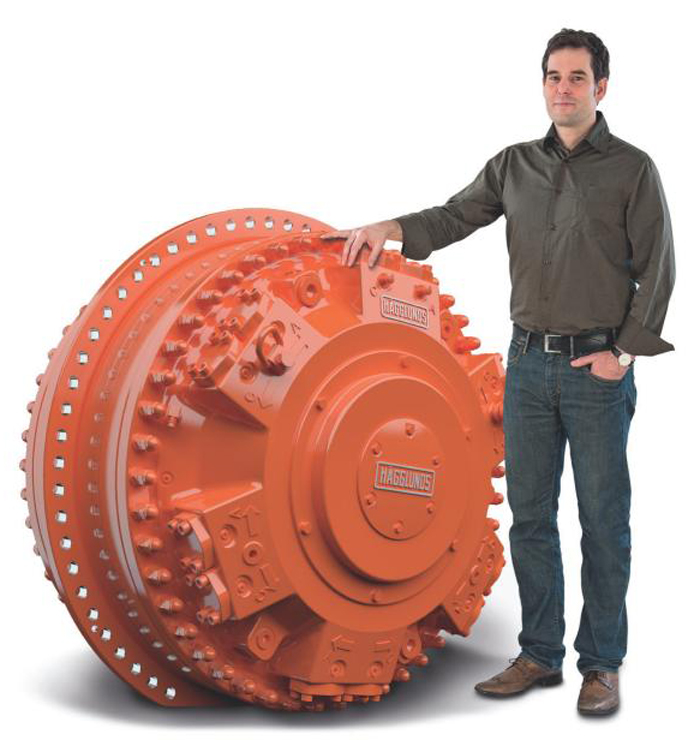 |
Just 1.3 meters in height, the CBM puts more punch inside smaller dimensions. |
Smart freedoms
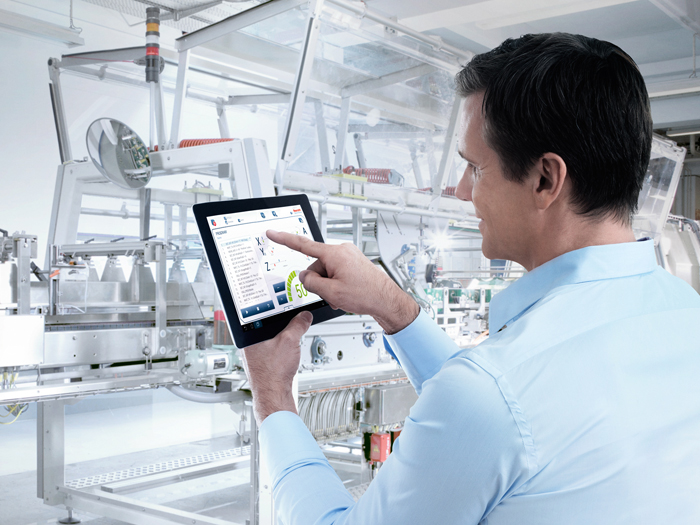 |
Manufacturers of machine tools are increasingly turning to software engineering to implement customized software functions – in part to set themselves apart from the competition. That is why Bosch Rexroth is introducing its Open Core Engineering concept to close the gap between PLC and IT automation systems and to increase the degree of freedom in software engineering. Here manufacturers, when programming HLL-based applications, have complete flexibility in accessing the core of the IndraMotion MLC and IndraLogic XLC systems. As a result, specific control functions for real-time applications can be implemented independent of the control program. Users can also use high-level languages to write their own software functions, which can then run as real-time applications, close to the hardware, right on the controls. They can also run non-real-time on external units such as PCs or smart devices. Innovative functions – and even those that require expanded access to the core program – can now be realized by machine builders. The know-how built into the app is protected at the same time.
|
Using Open Core Engineering makes it possible to integrate smart devices seamlessly into the automation concept. |
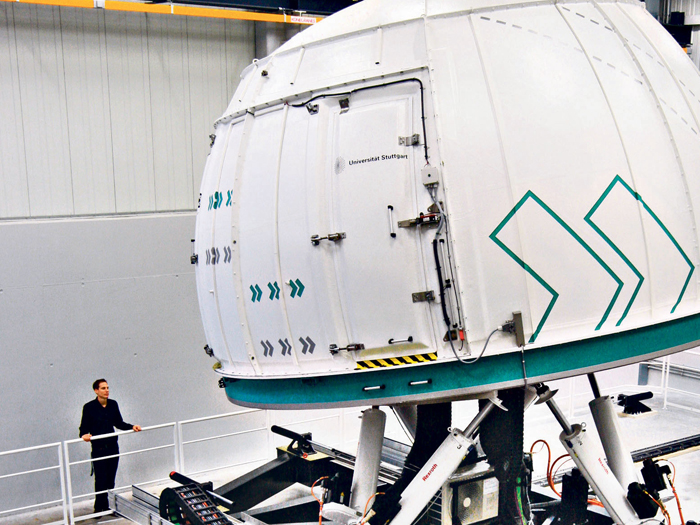 |
Driving on stilts
Europe’s largest and highest-performance driving simulator went into service at the University of Stuttgart in June 2012. Located inside this dome, weighing 1½ tons and built from carbon fiber, is a full-size car. Twelve video projections create a virtual traffic setting where new instrumentation, control systems, and driving assistants can be tested. The object is to enhance driving safety and lower fuel consumption. To achieve this, the capsule is driven by a complex motion system built by Rexroth. It achieves freedom of motion along eight axes, maximum velocity of three meters per second, and maximum acceleration of five meters per second squared. Thus the test driver experiences “motion” quite realistically, including acceleration, deceleration, and other forces – such as potholes in the road surface. |
The simulator lets the driver feel every virtual pothole. |
AWD as needed
A hydrostatic supplementary drive for trucks, made by Rexroth, is the efficient alternative to classical all-wheel drive. Weighing about 400 kilograms less than mechanical AWD, the Hydraulic Traction Assistant increases profitability thanks to higher payloads and lower fuel consumption. |
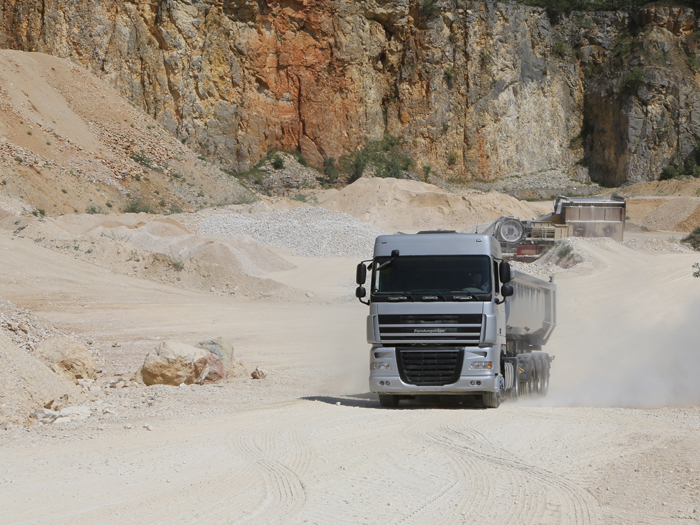 |
HTA: an all-wheel drive system that saves fuel and boosts payload. |
|