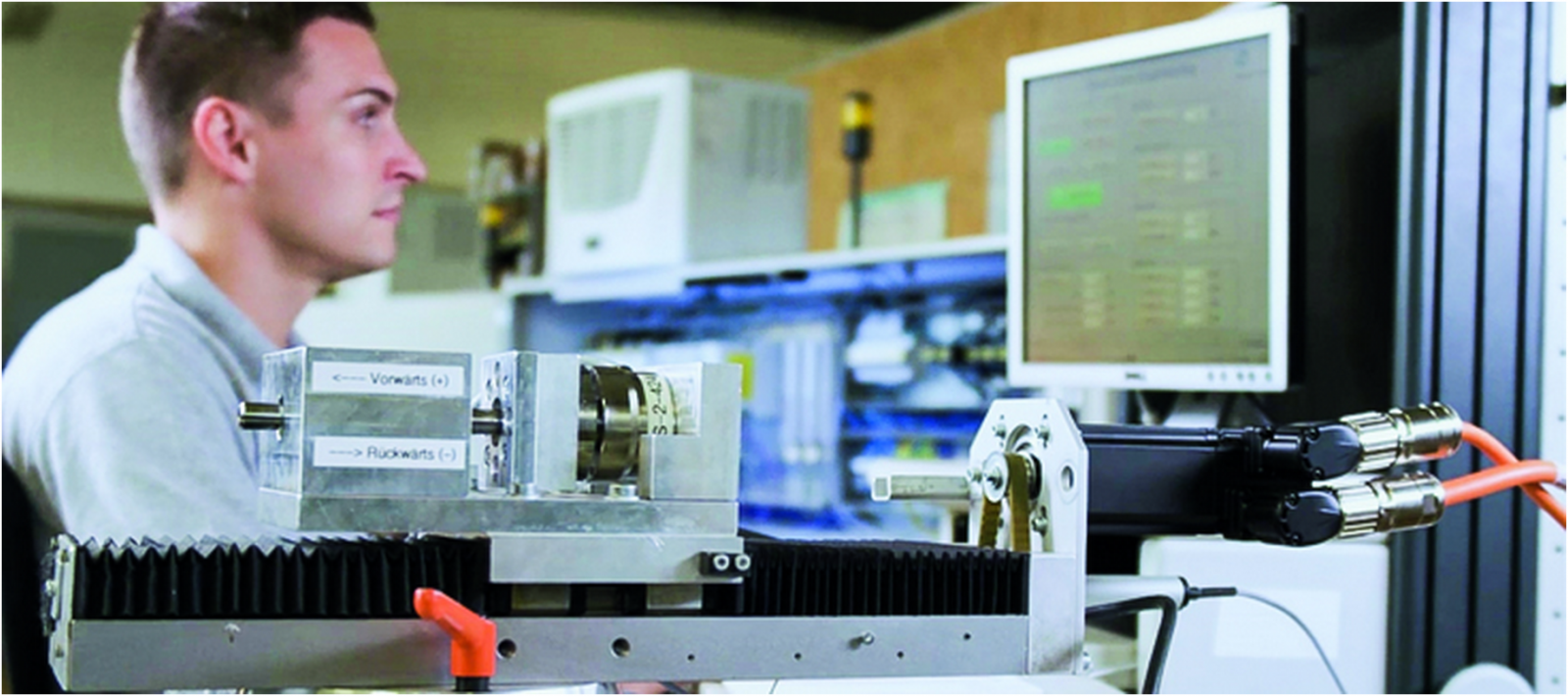
Thanks to Open Core Engineering, Kraus Automatisierungs-Technik GmbH can quickly program made-to-order test benches for its customers – without having to write a single line of PLC code.
Quality is one of the essential success factors for companies all around the world. That is why they put their faith in automated testing processes, including regular life cycle verification, fatigue testing and materials inspections. The machine builder has to match the testing units and instrumentation to the needs of each individual customer. Many employ the LabVIEW software package made by National Instruments for this function. This graphic programming system is always used whenever it is necessary to acquire and process measurement data and to integrate the instrumentation needed for inspection purposes.
One task – one user interface
Kraus Automatisierungs-Technik GmbH (KAT) also banks on LabVIEW. This company, located in Hassfurt in Germany’s Lower Franconia region, manufactures test benches for the automotive industry and other sectors. They are used to test mechanical elements’ service lives under the most realistic conditions possible. Until recently, the employees at KAT, in addition to programming using LabVIEW, also had to write a PLC program for the actual operation of the machine. This was both complex and time-consuming. In addition, the programmers had to have in-depth knowledge of both systems and had to use two separate user interfaces. That is why KAT sought an integrative solution. It can write programs for test bench automation without having to leave LabVIEW. “We have this option now with Rexroth’s Open Core Engineering,” says Stefan Besendorf, CEO at KAT. The new Open Core Interface technology makes it possible to program machinery via the LabVIEW software, without having to write a single line of PLC code.
“With the adoption of Open Core Engineering, we are now working with fewer user interfaces. That is both efficient and minimizes the risk of error. A single programmer has the entire project under his own control. This means that we are far more flexible in manpower planning,” Besendorf explains. Seamless and complete inclusion of the control and drive function in the LabVIEW development environment makes possible programming using LabVIEW only. This simplifies and accelerates the commissioning of customized testing equipment and instrumentation. KAT’s customers also profit from Open Core Engineering. They can use LabVIEW to make modifications to a testing machine themselves, without being familiar with PLC.
Reduced complexity
This degree of efficiency when programming instrumentation and test systems using the Open Core Interface is achieved by Rexroth with the aid of a Software Development Kit (SDK). With its help, and in conjunction with the IndraMotion MLC and IndraLogic XLC control systems, users can access control functions right from their application program. The programmer uses a supplementary package to import these libraries into LabVIEW and thus has more than 550 virtual instruments (VI) at hand.
KAT uses this new freedom, for instance, to execute the jog mode, but also for travel at velocity, position regulation, or switching on and off the corresponding drive regulator in LabVIEW. The signals generated by the sensors and actuators, wired to the PLC input and output modules, are available immediately. “Everything is programmed from beginning to end. “We only have to integrate the VIs into a class. That lets us form chains of steps for the actual machine processes,” explains Uwe Schweinfest, a developer at KAT. “And we can reutilize our work in later projects without major effort.” |