|
Company News
 |
Rexroth drive & control:The path: quick, short steps |
2016/03/07 |
|
With its dual strategy, Bosch Rexroth is focusing on economically viable Industry 4.0 solutions. |
As automation specialists, Bosch Rexroth has built “decentralized intelligence” into their products since the end of the seventies. At that time the company was the first to market purely electrical servomotors. It worked intensely on multi-axis controls and thusgradually displaced centralized intelligence which controlled a large number of mechanical components. This development gave rise to an interim plateau embodied in a number of products worthy of mention : the intelligent IndraDrive Mi, operating without a switchgear cabinet;the Open Core Engineering interface technology |
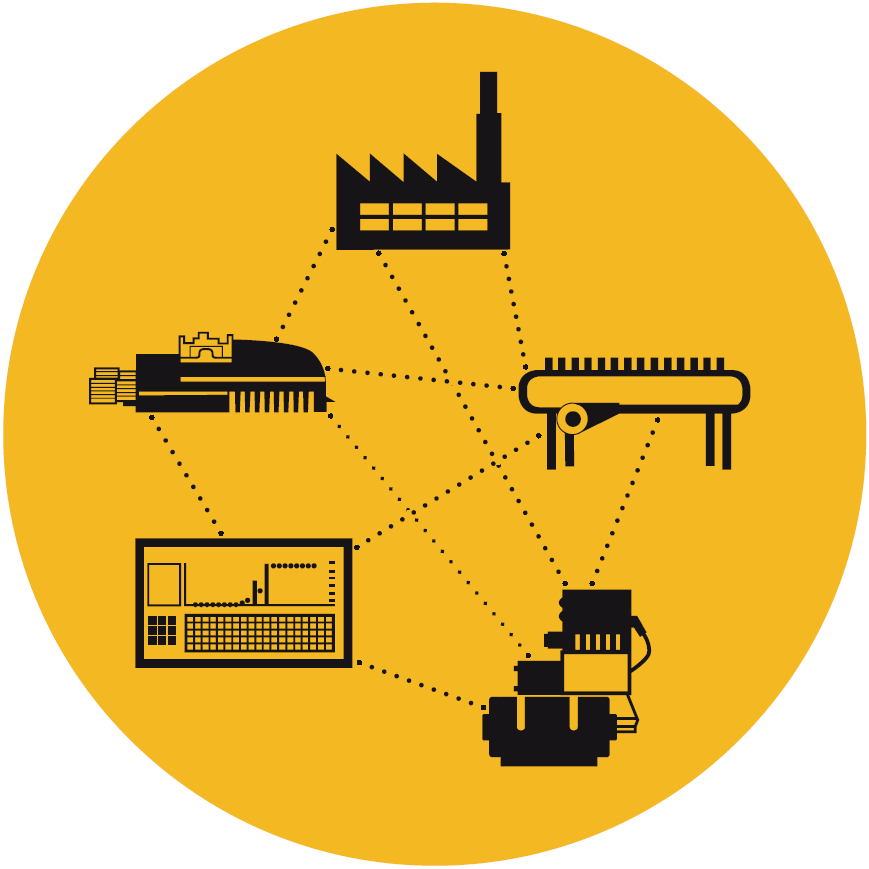 |
opened up completely new degrees of freedom with its extended access to control cores and links PLC automation with information technology;the latest generation of IAC MultiEthernet control valves lets mechanical engineering companies use intelligent hydraulic drives with uniform hardware in the most varied of automation environments.
This know-how was also applied to the multi-product line for our own production facility, manufacturing many different versions of hydraulic valves. This line has received the “Industry 4.0 Award.” It incorporates networkable products from all the drive and control technologies. Intelligent assembly stations not only adapt individually to each operator but also user RFID tags to communicate with corporate IT. This entails the application of identification and data transmission systems such as the ID 200. All the tools are connected via the data. This led to a ten percent increase in productivity and a 30 percent drop in stock levels.
Even the products painted at our own motor painting facility in the Swedish town of Mellansel “talk” to manufacturing control using RFID chips. Each motor automatically transmits to the network – with no physical contact – its current location and the operations still to be performed. Thus it is easy and economically feasible to make up products coated and painted to individual customer specifications. Customer service is also goal-oriented and performed at exactly the required time.
In projects such as the multi-product line or its own paint shop, Bosch Rexroth gained valuable experi-ence before these solutions were offered to custom-ers. “We are both front-running users and suppliers in the world of networked manufacturing,” is how Steffen Haack, member of the Board at Bosch Rexroth, explans this dual strategy. “This is how we evaluate technical options and implement what makes economic sense in quick, but moderate, steps.”
The experience thus gained then supports developments such s the new Online Diagnostics Network package of services (OdiN). This system continuously monitors the operating states of hydraulic systems and can initiate necessary maintenance and repair work before component failure causes downtime. This is of special interest to the operators of large plants such as those found in the paper-making, mining and offshore industries, where a standstill brings about high costs. The ABPAC hydraulic unit condition monitoring system also lets users keep an eye on current system status through recognized smart devices and plan maintenance work accordingly. |
|
Back |
|