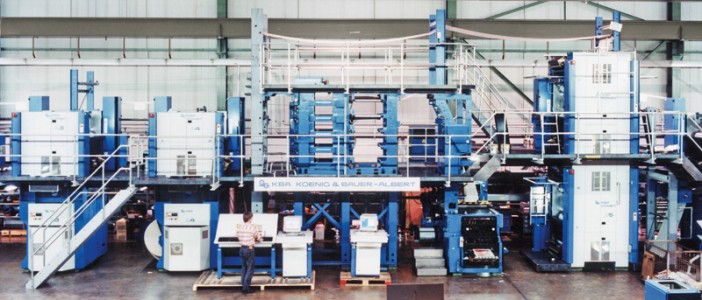
It was almost 20 years ago that Bosch Rexroth launched a revolution in the printing trade, sending many mechanical parts out to pasture. This innovative concept, the shaftless drive, helps print products stand up to the onslaught of digital competition.
The most recent revolution in the printing industry was instigated by Bosch Rexroth in 1994 with the Synax 200 automation system. This innovation made obsolete a basic principle that had survived for centuries: the mechanical coupling of all the components in the press. An essential element in these connections is a continuous shaft, running all along the system. It drives and synchronizes – with great mechanical effort – the individual printing units. The disadvantage of this technology is the susceptibility of the mechanical components to wear and the great amount of work involved in adjusting the shaft and other mechanical elements. Production has to be shut down completely, even for small changes and repairs along the printing line. |
That meant that printing didn’t always run smoothly. It was high time for a revolutionary idea. The Synax 200 supplanted the wear-prone mechanical parts, relegating that synchronization and drive shaft to the scrap heap. Intelligent motors, communicating with each other via the sercos automation bus, now drive the cylinders and rollers without need for shafts. These are synchronized to an amazing degree of precision with the motion controls – so that even the most demanding color prints can be produced. In the past, the press spewed out waste paper while that shaft was accelerating to full speed. The shaftless printing press, on the other hand, is ready for immediate work. A new job order is printed correctly and without spoilage, from the first impression. Individual parts in the press can be activated and deactivated separately, thanks to this new technology. Once the printing plates have been changed out, seamless transition from one job to the next is possible. Moreover, friction has been reduced by eliminating mechanical components. This lowers energy consumption and is augmented by the use of high-efficiency motors. This efficiency boost and the time saved when setting up for a new job ensure that printed products continue to be competitive, even in the digital age. |
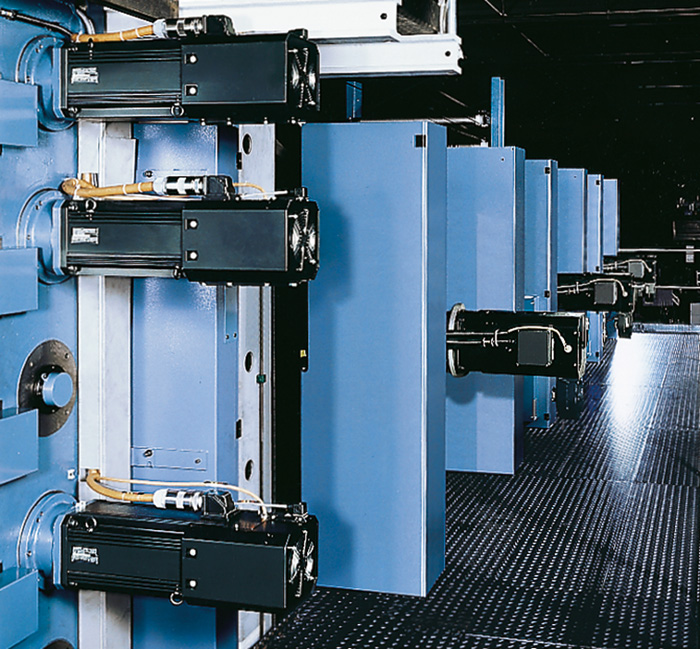 |
|