Case 1:Less is more
PCMC’s flexographic press – named “Fusion” – scores points with shorter set-up times and less waste product, thanks in part to Bosch Rexroth technology.
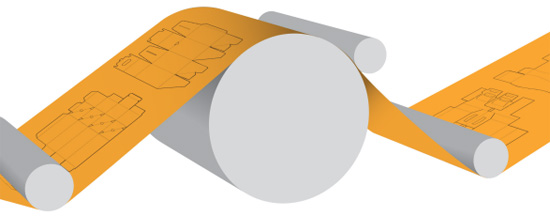 |
After all, the frills and trimmings shouldn’t cost more than the contents. With this challenge in mind, the Paper Converting Machine Company (PCMC) in Green Bay, Wisconsin, knuckled down and developed the “Fusion”. This is a flexographic press that works more efficiently than its predecessor, thanks to Rexroth’s drive, control and linear guide technology. “This sector began demanding shorter set-up times to lengthen productive printing cycles”, says David Wall, PCMC’s head of development for printing, coating and laminating. “Print shop owners want to save both material and time.”
A brief pit stop
The Fusion, equipped with the IndraMotion automation system and servo drives supplied by Rexroth, fulfills these requirements. It utilizes either 17 or 20 shafts, depending on the number of inking units. Seven further shafts serve as paper guides and control web tension between the feed and take-up rolls at the beginning and end of the machine. Each “Fusion” consists of a central printing cylinder between 2.4 and three meters in diameter. It can be surrounded by eight or ten printing units, each with two cylinders. These transfer the image and the ink to the material being printed. The cylinders are powered by IndraDrive M servo drives and gearless drive motors in the IndraDyn T series. Making things quicker and easier – that was the criterion for selecting the control unit. The MLC IndraMotion can synchronize machines with up to 64 shafts. Time-consuming manual adjustment for register and color for each individual deck is now a thing of the past. An integrated visual inspection system aligns the registration marks in no time at all, ensuring that individual colors are exactly congruent. Algorithms kept in memory help the printer cope with complex jobs. The result: After a roll of paper has been changed, the flexo press is back in operation far more quickly. The control system determines whether the printing cylinders are perfectly positioned, on the basis of the data stored in the drive units. An operating mode called PrintSense, developed by PCMC, makes use of this mode. It brings together the printing cylinder and the applicator roll in each printing unit with great precision. The press is then ready to roll.
Integrated safety features and an energy recovery system provide the “Fusion” with an additional competitive edge. Energy that used to be wasted when the shafts were braked is now recovered and returned to the system. A further positive factor:“While the printing plates are being changed, an IndraDrive function called ‘Safe Stop’ securely holds the shafts in their correct positions,” explains Wall. “In the past we had to incorporate a braking or locking mechanism, and that meant additional parts.” |
An efficient modular system
Fewer components mean lower costs – the “Fusion” sets new standards in this regard, too. By using intelligent drive technology, PCMC has managed to whittle down the number of parts required by almost 60 percent when compared with the previous model. This is because only two different motor sizes are now needed to drive the eleven machine shafts. This is achieved by installing IndraDyn T gearless motors, available from Rexroth’s comprehensive range of off-the-shelf modular components. |
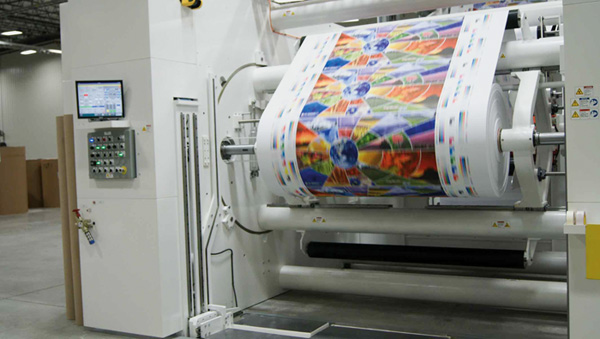 |
These liquid-cooled motors consist of separate stators and rotors and can achieve maximum torques of up to 13,800 Newton meters, accelerating the Fusion six times faster than in the past. “The multitude of standard motors is one of Rexroth’s major strengths,” emphasizes Doug Anderson, a sales engineer at the CMA/Flodyne/Hydradyne group, which specializes in system integration. When selecting suitable parts for PCMC, the experts went for one motor to actuate the large printing cylinder, which has to come to a standstill within ten to fifteen seconds. They chose a different motor for the image and inking cylinders, which differ in width.
A safe frame
To ensure that the cylinders are solidly and accurately fixed in position in spite of the high acceleration forces involved, PCMC also asked Rexroth to supply the linear technology. The performance requirements are stringent here. Once a print job is finished, the printing and inking units are moved back and forth, next printing cycle begins, they have to be firmly in place and must lock the printing and anilox rolls securely. This is the only way to print each color precisely, even at maximum rotation speeds. Highly accurate ball screw assemblies and four ball track systems are used in the “Fusion” to provide the required flexibility and stability. These components are compact, withstand high loads and function faultlessly for thousands of hours – with next to no maintenance. “Under no circumstances may the mechanical parts start moving randomly around the press, since this would have a negative effect on the print image,” says Wall.
“The ball screw assemblies and ball track systems supplied by Rexroth give us the stability we need to maintain the clearances and tolerances the Fusion requires.” PCMC has delivered the first of its new flexo presses to its customers – and they have met with an enthusiastic reception. Dave Wall knows why: “Improved set-up times and clearer system layout make it a lot easier to increase productive printing time. These benefits, in conjunction with the energy savings involved, contribute to the success of the new ‘Fusion’.” This concept lays the basis for attractive and appealing packaging that turns a stroll through the shops into a real shopping adventure. |
Case 2:Actively implementing change.
The staff at Deutz AG has introduced lean production methods to their daily work routines by implementing the Rexroth EcoShape tubular framing system. They are now able to assemble new equipment simply and quickly in a dedicated workshop.
Deutz not only arranges regular workshops but also relies on a kaizen workshop right in the middle of the production hall. That space is named after the Japanese production philosophy centered on continuous improvement. |
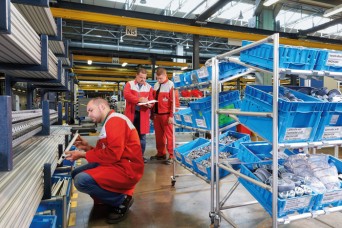 |
No room for waste
At this location the company manufactures engines in one of the world’s most modern factories. Their customers install Deutz drive units in mobile work machines, agricultural equipment or ships. Individual customer requirements are varied and demanding. Production rates are high; a new engine leaves the factory every 90 seconds. The manufacturing section must be quick to react to new situations if it is to maintain output at such a high level. This is why staff members always have access to the kaizen workshop situated at the center of the engine production facility. This facilitates assembling new operating equipment adapted to existing working processes. Workers can now test their optimization ideas to see if they are ready for factory use. This is done on the trial assembly line set apart for this particular purpose. Regular production need not be interrupted.
New operating equipment every day
Extensive stores of components from the EcoShape tubular framing system serve as the basis for the workshop. Rexroth’s sales partner, PTS Automation, supplied the components and also assisted Deutz in setting up the first items of equipment. The people at Deutz were delighted at how easy and quick it is to implement the “continuous improvement process” in daily work routines by using EcoShape. Hardly a day passes without new operating equipment emerging. “The number of possible combinations leaves nothing to be desired and is one of the reasons why this system sets itself apart from others,” says a happy Laakmann. The 19 different individual components can be assembled error-free with a joining technique which follows the poka-yoke principle – a fault-prevention principle that was also imported from the Far East. Depending on the application involved, the assembly line workers can also draw upon two completely compatible Rexroth lines: “Manual Production Systems” and “Basic Mechanical Elements”. The finished units are made of robust aluminum and are ready for immediate daily deployment. |
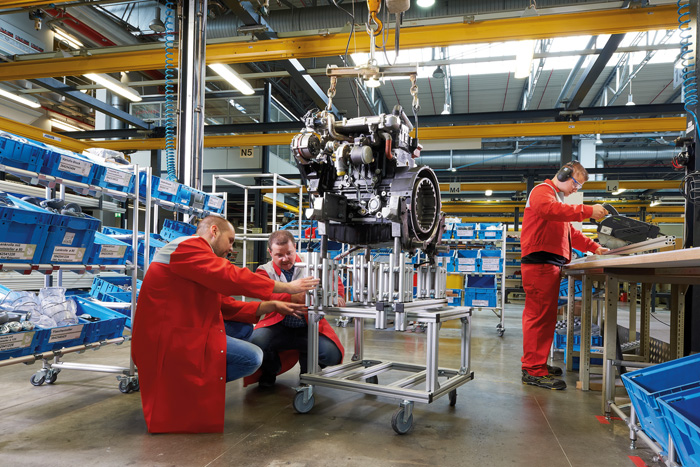 |
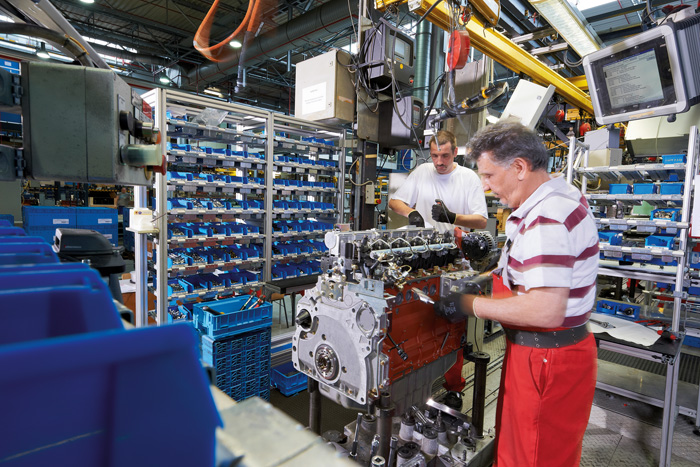 |
Geared up for the future
The number of possible applications is equally diverse: their workers, for example, constructed a support rack on which engines are moved to the workshop, ready to test mounting equipment there. This innovation means that transportation no longer requires undue physical effort. It is exactly this kind of exertion-reducing equipment that makes the EcoShape system worthwhile, not only now but in the future as well. |
Case 3:On the stick
The John Lewis Company, a Canadian manufacturer of the sticks used in ice cream bars, cuts energy consumption by 70 percent in one process step thanks to variable-speed pump drives.
A large part of these wooden sticks is supplied by the peeling plant at John Lewis Industries, located in the Canadian province of Quebec. Here more than 26 million ice cream sticks roll off the belt every day. Ever since 1920 this company has supplied leading ice cream makers all around the world with sticks made of birch, a wood that lends no taste of its own. The company draws upon sustainable forestry certified by the Forest Stewardship Council (FSC). But this supplier also wants to keep energy consumption during production as low as possible. |
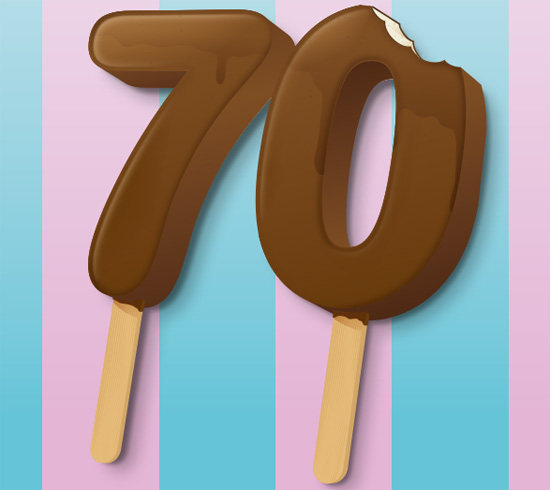 |
Sustainable forestry, eco-friendly production
That is why the firm launched an optimization project for the production process. The company consulted with energy efficiency specialists from Bosch Rexroth to take a hard, close look at the power unit for the hydraulically driven axes at the wood receiving station. There an automatic lift device raises the trunks and moves them into the peeling mill. If there are any disruptions in feeding, the crane – which is powered by the same hydraulic unit – frees up the jammed trunks and sends them on to the production line. To ensure that the operator could always respond quickly and flexibly to carry out this procedure, which is initiated manually, a constant-displacement pump continuously ran at full power in the past. The flow that was not needed was returned to the tank. At partial load that unit drew 12 kilowatts in this operating mode and at peak loads up to 20 kilowatts.
Savings: 70 percent
In their efforts to improve this unsatisfactory efficiency level, the specialists at Rexroth turned to the Sytronix SvP7000, a variablespeed pump drive. Its intelligent IndraDrive controls lower the rotation speed during idling phases or when operating at partial load, delivering just the amount of flow actually called for by the crane operator. This conversion brought about instant success. When running at partial load the hydraulic power unit now uses just two kilowatts – a 70 percent energy saving. The conversion itself was fairly easy and uncomplicated. Predefined functions and open interfaces for command level communications simplify integration, even into pre-existing systems. Users need not carry out any extensive programming. They need only assign parameters to the predefined regulators.
And it’s quieter, too
Energy is one factor but an acceptable working environment for the employees is just as important. “We are not talking just about energy savings, but also about considerable noise reduction and better system response,” explains Stéphane Pronovost, project manager at John Lewis Industries and responsible for rebuilding the system. That’s because the Sytronix reduces, on the one hand, average noise emissions by up to 20 decibels – without any additional noise abatement measures. In addition, regulation following demand also improves operator control. With the highly dynamic matching to real consumption, the integrated regulators compensate for the peculiarities of fluid technology so skillfully that the operator need not undertake any adjustments. What’s more, the crane now responds more sensitively and is more productive.
Standard for the future
In addition, Sytronix reduces the amount of cooling required since the hydraulic fluid heats up less than in the past. This both extends the service life of the hydraulic fluid and further reduces energy requirements. “I hope that this technology will become the industry standard for all hydraulic power units in the future,” Pronovost stressed. John Lewis Industries is making its contribution and is even now examining the feasibility of converting another power plant. |
Case 4:Reliability writ large
Chinese engine manufacturer CSSC-MES Diesel has adopted modular systems and halved delivery periods for its large marine diesel engines.
Large ships need powerful drives such as those built by Chinese engine manufacturer CSSC-MES Diesel Co. Ltd. (CMD) in Shanghai. That firm manufactures slow-running, high-power diesel engines – boasting cylinders 980 millimeters in diameter, turning at 97 revolutions per minute, and delivering 50,000 kilowatts. Their operational reliability is highly dependent upon vital control devices such as valve boxes and emergency control panels on the ship’s bridge and in the engine room.
A single supplier for the entire system
When the market started to boom, the delivery and assembly of these subsystems were not as punctual as CMD had hoped. That is why the company began looking for a more feasible solution. “Assembling valve control boxes is an elaborate process that requires great care and usually has to be carried out within a limited period of time,” explains Zexin Fang, purchasing project manager at CMD. |
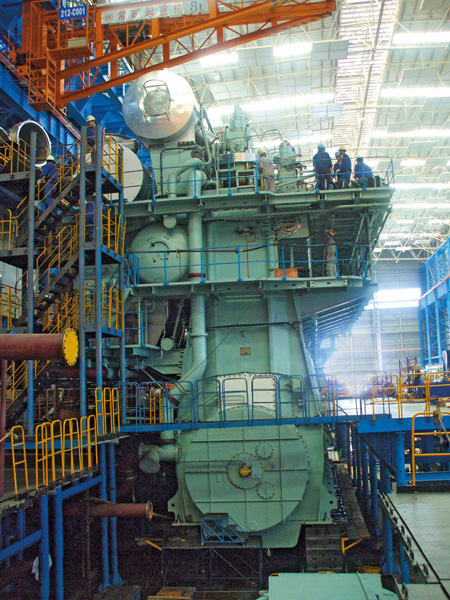 |
“That prompted an intensive search for a qualified supplier who could reliably handle all this integration work.” It was at exactly the same time that one of the firm’s suppliers converted to modular system concepts: Bosch Rexroth.
Up to that time the company had supplied a variety of pneumatic valves and the critical variable injection timing units. The latter control exactly when the fuel oil is injected into the cylinders; they also start, stop and reverse the engines. This change of direction uses pneumatic reversing cylinders developed especially for this application. CMD was so satisfied with this highly reliable collaboration that it charged the supplier with assembling the subsystems and delivering them on time. The supplier, in turn, quickly introduced decisive optimization ideas. At the Kangqiao assembly plant, located in Shanghai, Bosch Rexroth employees who specialize in marine technology have the expertise needed to assemble the valve control boxes. Adhering to the customer’s specifications, a number of valves and all the piping are integrated into a single cabinet. Thus the valve control box which CMD receives is entirely modular in its design.
Saving time and money
Closer collaboration also boosted efficiency. In the past the engine builder had to select the matching piping and housings for each of the individual valve components and, as well, find the appropriate suppliers. The company also had to fit the valves so that the boxes could ultimately be assembled. Ever since Rexroth began delivering the complete module, the customer’s throughput time has been cut in half – from as much as four months to just two. “We have taken the inlets and outputs for electrical power and air and matched them exactly to the housing,” is how Yuan Wang, pneumatic applications manager at Bosch Rexroth, explains the time savings. “As a consequence CMD, right after delivery, can simply connect the piping – laid according to drawings – directly to the housing. The valve control box goes into service immediately. That saves a tremendous amount of time.” And the collaboration itself cuts costs, as Zexin Fang emphasizes: “The improvements have reduced overall costs for the project by five percent.”
Continuous improvement
Rexroth is recognized for its wideranging know-how and decades of experience in the field of control engineering. These both paid off while implementing a variety of applications. |
|